Premier Pathology Laboratories
In the highly-regulated environment of US pathology, evidence is the lifeblood for documenting compliance with regulations. Retrieval of the right documents to verify that a lab operates in compliance is essential to satisfy on-site inspectors.
Not being able to pinpoint these documents can mean the difference between passing and failing any one of hundreds of regulatory requirements assessed during an on-site inspection. Failing to pass some regulatory requirements can jeopardize a lab’s license!
To tackle this issue, a California firm, Premier Pathology Laboratories, Inc. - which uses a dozen Apple Mac workstations and 2 Mac Mini Servers for its operations - has turned to DocMoto, to manage its laboratory procedure documentation.
According to the lab’s information technologist, Dave Hanks, “Since we opened in 1998 we had used Macs and AP Easy - a pathology reports electronic medical records (EMR) system, for management of patient data. Therefore, we knew well the advantages of controlling data via a central document management system. Yet, our laboratory’s procedure manuals sat on a bookshelf, in 3-ring binders, printed out as hard copy from Microsoft Word documents. The Centers for Medicare and Medicaid Services regulates laboratory testing with Clinical Laboratory Improvement Amendments (CLIA regulations). These include a requirement that all laboratory procedures be fully documented. Furthermore, the procedure documents must be kept up-to-date and reviewed annually. Of course, when a lab procedure changes, its related documentation must also be revised, reviewed and approved by the Medical Director. All retired lab procedures must be retained for two years.
“Our biggest challenge was to find the most recent source document to modify. Multiple versions of many lab procedure documents were stored on various workstations depending upon who created the original and who modified it last. After thirteen years in business and dozens of hardware, software and personnel changes the process of finding the right document to modify was nearly impossible. Frankly, it was easier to grab the manual from the shelf and retype a few pages and replace them instead. While we needed and wanted an electronic document management system, the transition from paper to electronic lab manuals was such a huge task that we never got started. The result of a recent, on-site inspection forced us to reconsider our lab procedure documentation method.”
Dave explains: “When the day of the unannounced but long overdue inspection finally arrived we learned that the inspection rules had changed; the inspection team leader said: “We were now in the era of evidence of compliance.” Because the annual inspection was so late, we faced a much more rigorous validation process that was based on a new set of rules that had just gone into effect. The three College of American Pathologists (CAP) inspectors simply asked for copies of every lab procedure manual. Unlike previous inspections, they would sequester themselves in an office and scoured our fourteen procedure manuals to verify that we had documentation that proved that we were in compliance.”
“During all previous inspections we played an interactive role in the inspection process; that is, the CAP inspection team would split up and work with our staff to complete the inspection. Together they progressed through the CAP regulatory checklist and when requested one of our staff would retrieve an appropriate document to verify compliance. This worked because we knew which lab manual to search. At the end of this particular day, it was obvious that our hard copy lab procedure manuals did not meet the inspector’s expectations.”
Prescribing DocMoto
“It was our worst inspection result ever. We were cited for several deficiencies including failing to respond to the entire question set covering regulations on computing! Although I knew that I had completed the checklist, somehow it had become misfiled. (The first step in a CAP inspection is for a lab to review itself for compliance with the previous year’s inspection checklist. I had copied the entire computer section and responded to those questions by hand. I provided my answers to the lab manager who inserted it behind the entire lab inspection question set. Of course the inspectors saw the unanswered pages of the computer question set and concluded that they had not been completed.)
During the exit interview, we did produce some of the ‘missing’ documents, but even we faltered as we frantically searched our manuals by hand to locate documents for evidence of compliance. We did not find the missing computer section until two days after the inspectors had left. We obviously needed a better system to search our lab procedures and various regulatory documents.”
The clock was ticking…
“CAP requires a written response to all deficiencies within 30 days of an inspection. Each response must provide the reviewers with evidence of compliance (a new written lab procedure document or a copy of the existing lab procedure document) or a detailed response regarding how and when we plan to resolve the deficiency. The short timeframe prompted us to install a trial copy of DocMoto. We had high hopes that it would expedite our response effort.
With DocMoto our response process was vastly improved. Dave ‘parked’ a single copy of a blank CAP response template on the DocMoto server. From this one source document we downloaded and created multiple response templates as working copies for each response to a deficiency. After initially setting up these response documents they were saved [In DocMoto’s parlance: “checked in”] to a preliminary folder. Each preliminary folder was assigned to one of three workgroups. Members of each workgroup could “check out” a working response, review it, add their own text and comments edits and then “check in” the revised version for their teammates to review. During each step DocMoto maintained a complete version history and captured meta data including the names of everyone who retrieved, reviewed and modified the text for a response.
DocMoto let users compare different document versions, on one screen, to expedite the review process. If necessary, a previous version could be restored, allowing us to revert back in time to create a new master. And when a document remained “checked out” for too long, other team members could see who was holding up progress so they could push the document to the next step in the cycle. As each response was finished it was moved to a pending approval folder. Once there, our Medical Director could execute the final review and approval, or add comments for improvement and bounce it back to a pending folder. Because editing or moving a file can trigger email alerts to those who ‘subscribe’ to track a document, the emails could act as reminders to notify all team members when action is needed.
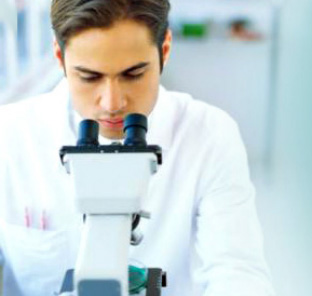
We finished our response a couple of days ahead of the CAP deadline so we had plenty of time to review and polish. Within a week of submitting our inspection responses we received confirmation that we rectified all of the noted ‘deficiencies’ and were once again operating in full compliance. DocMoto had served us well in this new era of ‘evidence of compliance’.
The system worked so well that we are now converting all of our hard copy lab procedure manuals to online manuals. The conversion will take some time due to the size of the task, but we can already access several lab procedure manuals as searchable pdf documents. The hardware and software needed to scan and convert existing lab manuals to generate searchable pdf documents is inexpensive (less than $500 per workstation) and quite beneficial. This text can also be copied and pasted into a new electronic version of the lab procedure document so the staff can avoid retyping the documents by hand. The new virtual procedure manuals can be viewed from any workstation in the lab.
As with many technologies, once you make the initial investment, you often discover many new applications. It didn’t take us long to realize that other business documents could be scanned and stored in DocMoto for virtual reference. A wealth of employee information is now stored within DocMoto. This includes hiring documents, tax forms, job descriptions, retirement programs and other important employee records. By using the DocMoto permissions options we create hidden folders that are only visible to those who are authorized to access these sensitive documents.
Because we are a medical business we also store patient data. Thus, we must also conform to the Health Insurance Portability and Accountability Act (HIPAA), which define security for handling protected health information. DocMoto’s individual and group privilege features will help us maintain compliance with HIPAA standards even if we open portals for the hospitals and physician offices we serve.
The pressures of unannounced, on-site inspections face every laboratory. With DocMoto, it is possible not only to facilitate compliance, but is possible to accelerate a response if and when needed.
This pressure of changing regulations is what led us to discover and try DocMoto and to formulate the thought that - come the next compliance inspection - we might simply hand the inspectors an iPad and let them access and search our new virtual lab procedure manuals to simplify their task of verifying our compliance.”